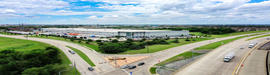
Advantages of Cross Docking in Supply Chain Management
With cross docking, a business can become more competitive through a variety of ways. One is the reduction of square footage necessary in a warehouse. Because products are not stored for long periods of time, all costs associated with storage are also reduced or eliminated. Additionally, cross docking makes for a simpler shipping relationship because fewer parties are involved.
-
Reduced Costs
One significant benefit to cross docking is cost savings—and not only by avoiding long-term storage costs. Because the product is not stored for lengthy periods or passing through numerous hands, there is lower risk for the product to become damaged and require replacement.
-
Decreased Shipping Times
Saving money isn’t the only benefit to using cross docking in supply chain management. Shipping times are dramatically reduced. Your company can work more efficiently by eliminating the need for multiple business relationships. And just one team can handle the warehousing and expedited shipping.
-
Improved Efficiency Through Better Inventory Management
With cross docking, the risk of inventory surplus is reduced. Stock is picked and shipped directly to customers, thus decreasing the time to ship items. You don’t have to keep excess inventory on hand to meet fulfillment expectations because shipping time is reduced. Employees can also assess damage quickly during the unloading process to improve product quality.