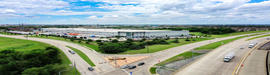
What Are the Common Components of Fulfillment Costs?
Look for several common components when calculating total fulfillment costs. These can include both statistical data and actual cost data. Below is a breakdown of what each component entails.
Statistical Data
- Annual net sales
- Annual number of marketing orders processed and shipped
- Total number of lines ordered on the marketing orders
- Annual number of boxes shipped by the fulfillment center
Cost Data
- Total cost of direct labor for all functions required to fill orders, including receiving, putting away, picking, packing, shipping and returning items
- Total cost of indirect labor, which is any labor function not classified as direct labor, such as supervision, maintenance, clerical and inventory
- Total occupancy costs, including lease amount, utilities, amortization and depreciation for material handling, conveyor and sortation equipment, and the warehouse management system
- Total cost of packing supplies required to fill orders